Cost Reduction Through Near Shore Manufacturing Optimization and Low Cost Country Sourcing
A major consumer products US company aimed to significantly reduce COGS through their OPEX manufacturing strategic plan. The company understood that in order to significantly reduce COGS, they needed to diversify their manufacturing footprint and simultaneously optimize the Product Portfolio, and Low-Cost Procurement and Low-Cost Manufacturing Practices.
SITUATION OVERVIEW
The company had a number of plants across different regions in the US but no international plants. The current manufacturing footprint could not sustain the market pressure caused by the lower prices of competitors with plants in Asia and Latin America despite all the cost reduction efforts. Driven by the new aggressive cost reduction mandate Senior Management decided to start up a manufacturing plant in Mexico to take advantage of the low-cost manufacturing labor in the country as a key strategic initiative to reduce COGS and improve EBITDA.
The company hired OnDemand Professional Network member Juan-Luis Munoz as the VP/GM of International Operations to lead this strategic endeavor.
APPROACH
The team first performed an assessment of the OPEX Current State, Product Portfolio, Manufacturing Network, OTC Lead Times (Order-To-Cash) and top spending accounts. The company graded poorly along several high-level OPEX critical elements:
- Fragmented and isolated improvement efforts
- Lack of manufacturing standardization and best practice deployment system
- People engagement, motivation and empowerment
- Structural misalignment
- Unstandardized KPI measurement and reporting
- Business macro flows not properly connected
- Obsolete manufacturing methodologies
Understanding the current state was crucial in planning a successful manufacturing plant in another country. Among other things, the team uncovered significant manufacturing practices being conducted with the use of “tribal knowledge” only. When some level of standardization of processes was found, this was executed by multiple individuals in different functional areas across plants– that was causing significant level of confusion and consequently affecting all improvement efforts.
The approach followed a proven concept – Current State Analysis > Gap Analysis > Future State Design across People, Processes and Manufacturing Technologies.
This was necessary to be ready to design the first international plant of the company. The Team agreed that they should jointly work toward an end-state where:
- Operations would have the personnel, skills and bandwidth to execute most modern manufacturing technologies when opening a new plant regardless of the geographic location
- They would manage OPEX standardization centrally
- The company would adopt the Balanced Scorecard to eliminate the lack of structural alignment and business micro flows disconnections.
The Gap Analysis outlined a good number of areas for improvement, but it was clear that the common factor was that the new operations organization had to increase the use of modern manufacturing technologies.
CRITICAL SUCCESS FACTORS
- LEGAL FRAMEWORK AND COMPLIANCE: MX Corp set up, gov permits, certs and contracts
- PEOPLE: HR plan, Union BA, knowledge transfer plan, perf eval system -PES, EHS
- PRODUCT PORTFOLIO AND ENGINEERING: Prod. Specs, BOM, Routings, Testing, MSA, DFMEA
- PROCESS AND FACILITY: Process Design and Validation, VAVE, PFMEA, PMS, QMS, IT & Coms
- MATERIALS, PROCUREMENT, LOGISTICS, ORDER ENTRY AND IMPORT/EXPORT
- FINANCE: FMS, Cost accounting, Taxes, Banking, Op Budget, Plant start up budget control
RESULTS
The new manufacturing plant started in less than a year successfully.
The company adopted several new best practices as a result of this project such as the new product and process validation and certification and the BSC (Balanced Scorecard).
These are the top 3 results:
- Reduction of the average lead times from 6 to 2 weeks (order-to-delivery)
- Labor efficiency increased from 72% to 95%
- Fully loaded labor cost reduction from $21/hr. to $4.50/hr.
And perhaps most importantly, the new operations organization was positioned to become innovation and OPEX leaders in the business.
CHALLENGES
People and skills – Training and knowledge transfer of new operations to another country was a big challenge. We had to implement a very comprehensive training program using tutors, skill matrix management and a different job category system based on job complexity and a set of KPI’s for each category. Job complexity analysis was key in this process. Once finished, we were able to understand very well the training and skills needed by operation as well as the DPMO (Defect Per Million Opportunity) to better plan our manufacturability, quality and reliability assurance plan. Tribal knowledge was always the enemy because it causes lack of standardization and many issues in training new personnel.
Manufacturing Footprint Optimization – This was achieved through iterative kaizen events. Footprint evolved from straight-line batch production cells to modular flexible continuous flow production cells. Space utilization improved significantly in terms of sales per square foot. However, the master scheduling process had to be revised to optimize changeovers, people utilization and total lead-time. This was very critical because all improvements you make on the production floor are futile if the rest of the operational practices never change such as supply chain, customer order validation, order entry, master scheduling, logistics, etc.
Machinery and tools – Every time a manufacturing organization experiences new market pressures, it needs to decide between evolution vs. revolution. Overall Equipment Efficiency (OEE) and Single Minute Exchange of Die (SMED) had to be learned and mastered by the engineering team along with a comprehensive predictive maintenance program (not only preventive) using advanced reliability methods such as MTBF (Mean Time Before Failure) and MFMEA (Machine Failure Mode and Effect Analysis). Using only a Corrective Maintenance Program is not acceptable.
Change Management – We had to develop a comprehensive program which included several sections such as the human side aspect, organizational dynamics, communications, change agents, new business practices, readiness, involvement, training and impact, among others.
Value Stream and Value Proposition Continuous Evolution – We had to develop the mantra of never be satisfied with the status quo, so this is something that is a big challenge, especially with people that are very complacent in their comfort zone of doing the same things over and over again.
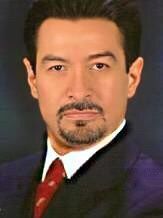
OnDemand Professional Network Member since 2021
Juan-Luis has 25+ years of experience starting up and leading multi-plant and multi-country business units in diverse industrial sectors (automotive, aerospace and consumer products) with high concentration in Latin America.
He practices a very decisive and assertive servant leadership through operational excellence, best in class business practices, team development and communication that has led to sustainable and profitable growth of public and private companies.
Juan-Luis is very well versed in restructuring undervalued and under-performing businesses through TPS lean manufacturing transformation, 6Sigma deployment, product portfolio optimization, low cost procurement, low cost manufacturing, innovation and speed to market strategies.
Experience in start-ups and turnarounds in private and public companies with global supply chain and operations.
Pioneer in TPS Lean Manufacturing, Operational Excellence, 6 Sigma, TOC, DFT, DOE Taguchi, Shainin, Shingo, K&T, 8D, PFMEA. APQP, DFM and other manufacturing technologies and improvement initiatives.
He is a Certified Lean Six Sigma Master Black Belt and he holds a BSE in Industrial Physics and Manufacturing Engineering and MBA from Monterrey Tech (ITESM) and EGADE Business School.
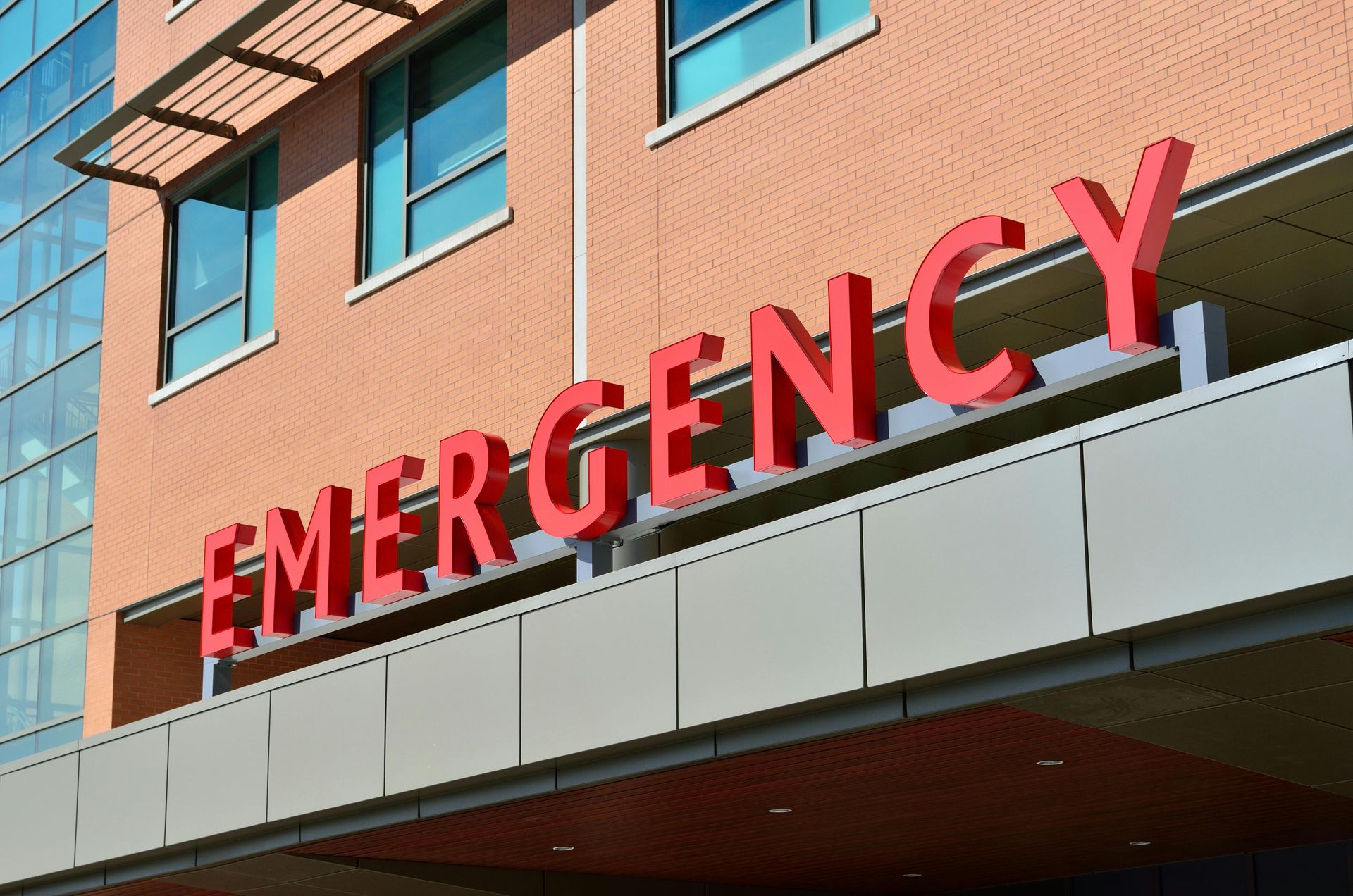
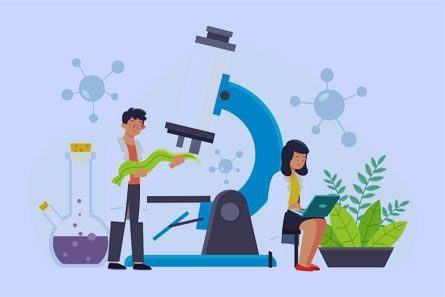
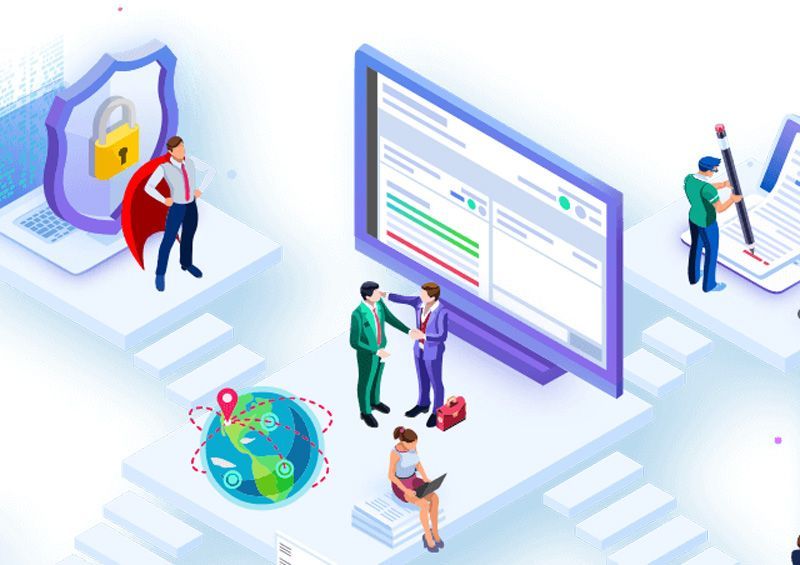
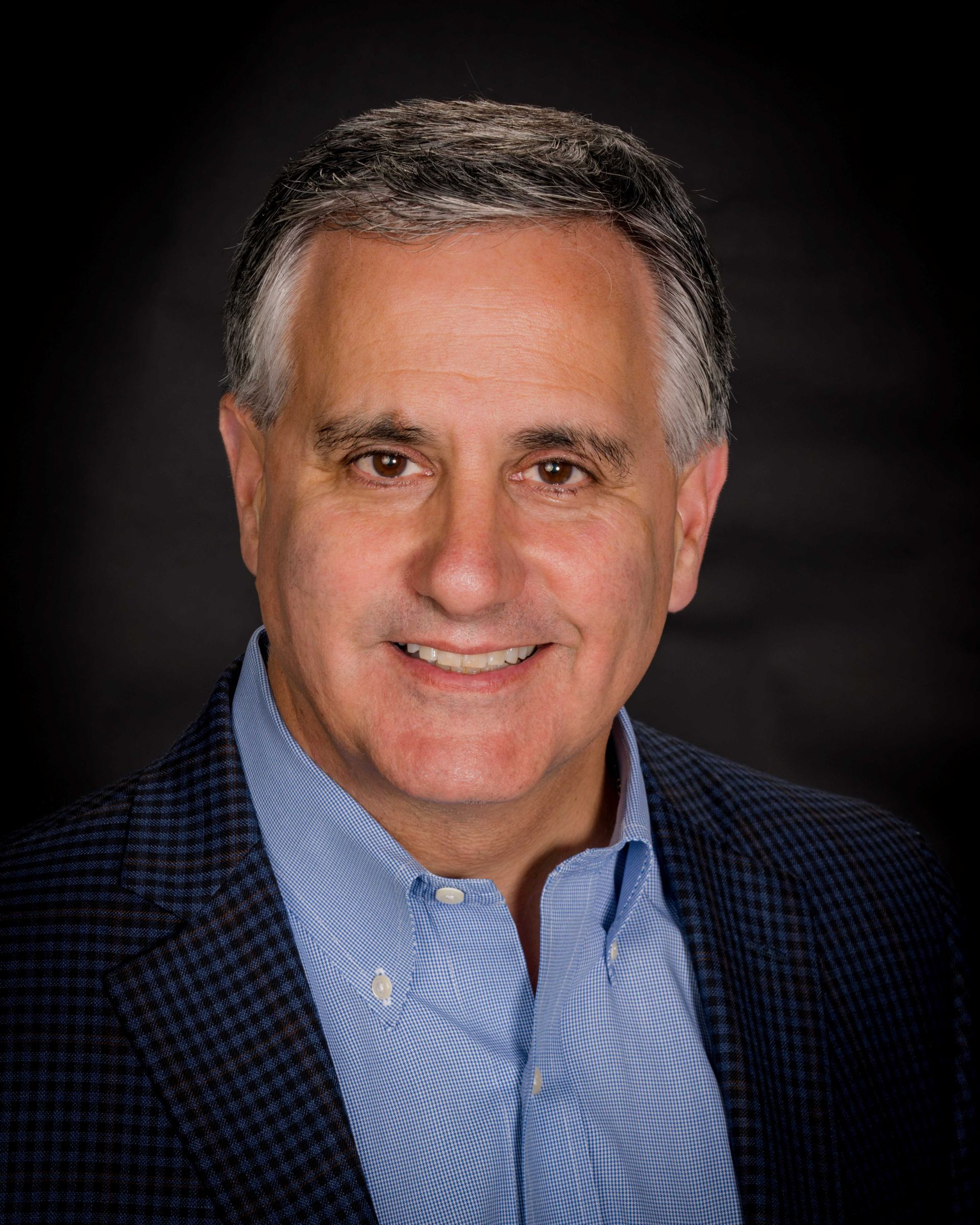
Tom Donatelli Joins OnDemand To Enhance Our Client Service Capabilities And Broaden Our Market Reach
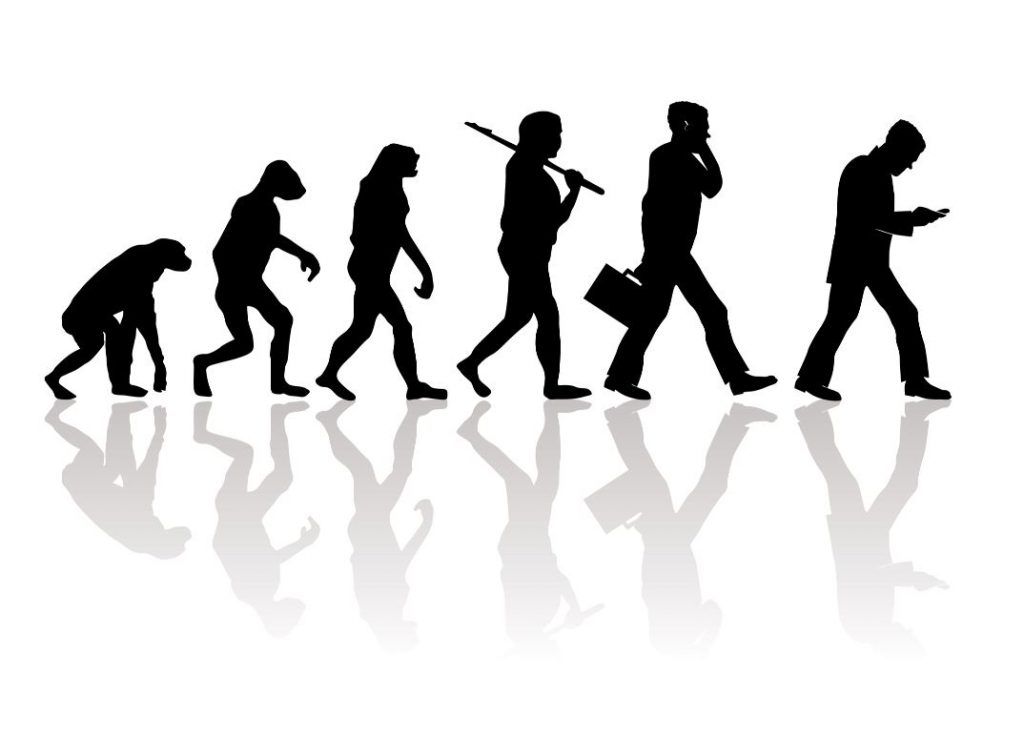
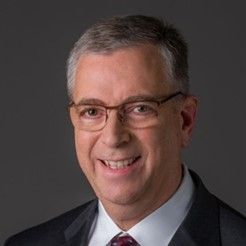
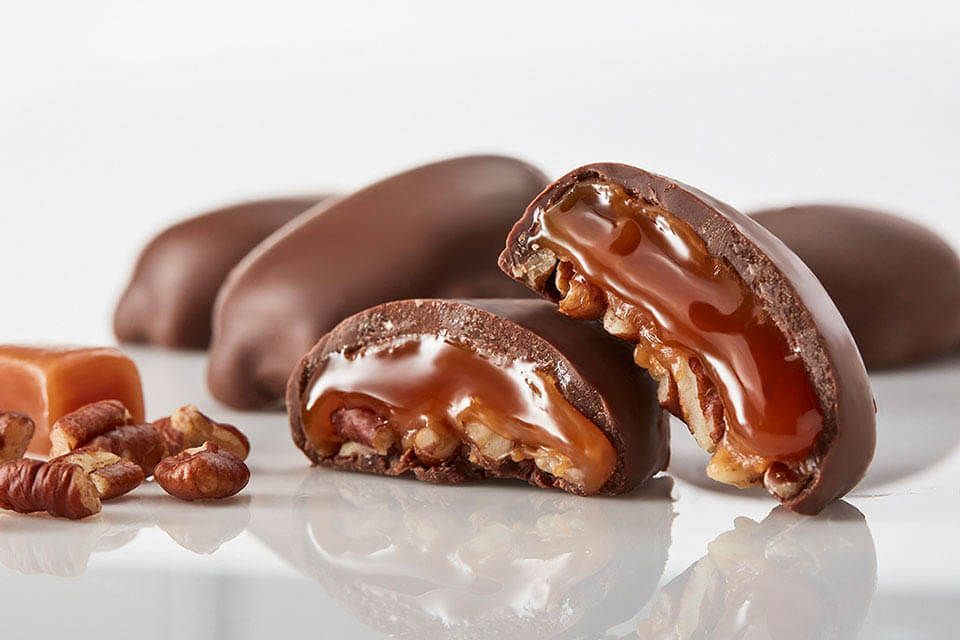